Wednesday, November 1, 2006
Staying Ahead
The high-tech marketplace is brutally competitive. Memory module business is no different. Most memory module companies set themselves apart and stay ahead of competition through innovative technology, creative cost-cutting measure, unparallel logistic advantage and unique process development through automation.
Steering towards automation means using techniques and equipment to achieve automatic operation or control. Automation is ideal for mass production environment. It increases product quality by minimizing human intervention which statistically listed as one of the major factors towards product failure. Automation also helps reduce the overall cost as a result of fewer product returns and customer complaints. More often than ever, adopting an automated solution has become one of the reasons a memory module company is still staying ahead in the race.
Human Error
In any production environment, human operators make mistakes. It is more so especially towards the end of the daily shift when working fatigue sets in, and the overall mental alertness level falls. The production monotonous process of doing the same action over and over again also contributes to the unconcious mistakes and misjudgement. Production test operators literally get fired for production mistakes like treating the bad or untested modules as good. As a result of these errors, many dissatisfied customers with their reputation and bottom line at stake continue to seek for alternate vendors who make better quality memory products.

Bad Solder Joints
High quality products is an objective that all memory module companies set to achieve. The big questioin is high quality comes at what price and by what mean? Some company spent huge fortune to improve quality but gain very little good results. Some companies refused to upgrade their aging equipment to newer ones to experience productivity gain and explore better end-results. The right investment strategy for most companies is simply to find a reliable production solution which can generate favorable returns at a fair market price.
Many memory module companies now believe that automating the entire production process is the key to achieve high quality product. Automation prevents human-error since machine can be programmed to do testing and sorting consistently no matter what time of a day. In fact, more and more module manufacturers are leaning towards fully automated solution regardless of whereabouts of their plant locations. Whether the company is located in California with higher worker wagers or in mainland China where cheap labors are concentrated, automated handler is still the only way to achieve high quality product within the shortest time possible.
“No matter what, machine unarguably is more dependable and eventually would save me more money by reducing costly product return,” said a production manager of a major memory module maker. He continued to point out that the out front investment in the machinery is paying off in no time with the instant productivity boost.
Improper Handling
Memory modules especially DDR2 Modules with Ball Grid Array (BGA) packages require proper handling and testing to avoid breakage. Grabbing, stressing and pressing the components on-board with one’s thumbs and index fingers to force it into the test socket is the key factor to part breakage.

As timing frequency gets higher, the old lead frame inductance of the TSOP package becomes obsolete. BGA package is used as a replacement to reduce the lead frame inductance. This BGA package has no physical leads but solder ball attached directly to the printed circuit board.
Handling module with BGA package is like walking on a tight rope. It requires balancing. On one hand, you do not want to press or force it too hard to break the solder joint. On the other hand, you also do not want to be too “protective” and miss catching a potential bad module with a weak solder assembly before shipment.
DDR2 BGA design has additional "mechanical balls" on the DRAM package. These are extra solder balls with no function at the four outer corners of the BGA package. They are purely for mechanical reinforcement and intend for normal handling including low-level shake and bounce. If a module with weak solder joints is overly “protected” during testing, the weak joints will only break during freight and causing it to fail in the field.

Eroding the conventional wisdom that machine tends to break part, automated handler surprises many with its well-thought-of design and delicate operation. Not only has it offered a special kind of soft-handling mechanism to minimize breakage, its vibrating effect during module insertion and transferring process also helps to shake off any module with weak solder joints. Auto handler may well be the “one-pass” system that can test and program the module as well as screen out any potential assembly faults. One engineer once said, “If the DDR2 modules (with BGA package) can’t withstand the mild shaking and module stacking during production test, they surely won’t last long when reaching the street.”
Prolong Socket Lifespan
One of the costly wear-and-tear parts for module production is the test socket. With the introduction of DDR2 modules, the lifespan of the socket has further shortened. Some companies spend a decent amount of money replacing the broken sockets far too frequent. The key reason is improper manual inserting technique.
DDR2 DIMM module has 240-pin edge connection. Insertion into its mating socket takes more force compare to its older 184-pin DDR DIMM sibling. “Assuming a 1/4 lb per pin insertion force will amount to 60 lbs of insertion stress. This insertion force will not only create fatigue to the human hands, but also creates a heavy mechanical stress to the socket and DIMM itself,” said Cecil Ho, the President and CEO of CST, Inc.

The best way to address this issue is to build a mechanical system to precisely and delicately push the device under test into the socket at the same angle and level of force each and every time. The end results of having such mechanical solution are far outweighing its cost. The operators will stop complaining of their hands hurting, the test socket's lifespan will be prolong by multiple times, and best of all, the overall test time will be reduced. The precision technique and matching pin-to-pin alignment cut down the false test error significantly, which would otherwise require unnecessary retest or repair.
Roboflex2 Handler - Flash Back
Several years back, CST conducted a survey with several major OEM memory module manufacturers in the United States and several key manufacturing managers were asked to list the importance of features on an alternative handler that does without expensive Pick- and-Place concept:
- Scratch-Free, and no mechanical stress on the module under test
- Module should not fall into each other in the sorting bin after testing
- Module should not be dragged on any surface during transfer from point to point.
- Handler must have minimal adjustment features and must be easy to operate.
- Change over from one type of module to another should be simple and straight forward
- Manufacturers also want the fastest handler for efficiency – when compared with the Pick-and-Place handler
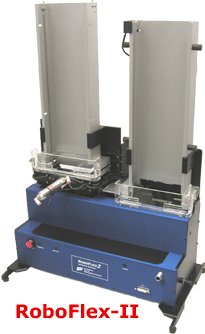
Researching and Designing Roboflex2 Handler
In order to offer an alternative to the "Pick-and-Place" handling concept, CST engineers studied various Pick-and-Place system and found one thing in common - in order to prevent inflicting module from possible mechanical stress and scratches after testing - CST’s engineers came out with the Soft-landing concept to buffer module from dropping after testing. In addition, the pneumatic control, Scratched-Free "Transfer Carrier" is added to piggyback DIMM module to the stacking system.
The winning concept satisfies all the “Pick-and-Place” conditions and yet provides a "scratched-free transfer system" with "output stacking system". After years of success implementation at many companies, the new handling concept is proven to be out perform the "Pick and Place System" at a fraction of the cost.
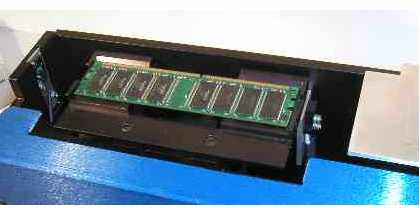
DIMM resting on Roboflex-2 Belt-less Transfer Carrier System, right under the carrier is the "Soft-landing mechanism"
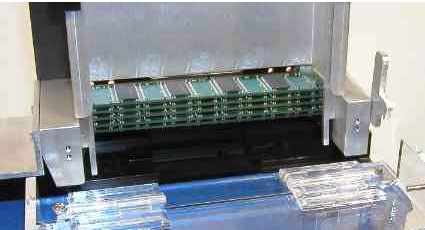
Roboflex-2 Stacking system (Modules are stacked upwards - by a special Elevator Platform)
In Short
It is no doubt that manufacturing automation has become a competitive edge to drive down production cost while improving overall quality. Hands Free Automation minimizes human errors, prevents module breakages, extends test socket’s lifecycle, reduces test time, and helps uncovering any potential assembly issues. All these benefits translate into cost saving and better quality control. Compete through automation is undeniably a winning strategy setting a company apart from the rest
By: DocMemory Copyright © 2023 CST, Inc. All Rights Reserved
|