Thursday, April 5, 2007
By this time, every memory module manufacturer should have a whole drawer full of “pulled” DDR2 chips and do not know what to do with them. For the past year, module manufacturers have been pulling chips out of non-working modules and replaced them with new memory chips to make the module work. Yet, they have no way to confirm that the “pulled” chip is really bad or just a bad solder joint. To do that verification, they would have to “reball” the BGA chip, test it and then reuse it on a new module. To most memory module manufacturers, “reball” is a new process to them. They neither have the equipment nor the know how to do it. Yet, they do have to seriously think about that when the accumulation has gone beyond control.
The Professional Reball Process
The proper reball process is listed in the flow chart:
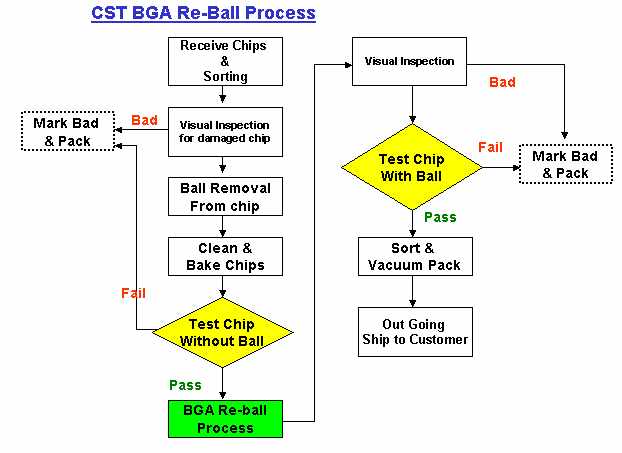
Visual Inspection
Visual Inspection is normally done under a magnifying scope. The operator should be looking for hairline solder bridges, hairline cracks, and also burnt marks. All those are indicators of damage chips that would be a waste of time on repair.
Ball removal
The old balls must first be removed. Soldering iron and solder wick is the best method. Flux are added to help the melting temperature and the easy flow and easy pick-up of the old solder residues. Sometimes hot air supply with the proper size nostril would also help.
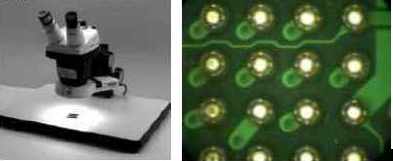
Clean Bake Process
After the old solder balls have been removed, ultrasonic cleaning is required to totally ride of contaminents and flux residue. Only high concentration alcohol or a non-abrasive solvent should be used for the cleaning.
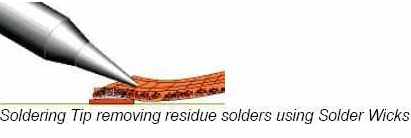
Once it is cleaned, the chip should be baked to dry. This is to eliminate the bubbling effect that might happen on the substrate. The baking process should be 24 hours under 70 degree C.
Test without balls
At this point, the chips should be functionally tested to take out the electrically bad chips. Since these are “pulled” chips, multi-test pattern test should be applied to weed out the hidden bad cells and non-functionalities. Since the balls have been removed at this point, the test socket should be of pogo-pin type to ensure contact on a flat surface (no ball). Only the good chips are put forth for the physical reball process.

The Physical Reball Process
The reball process consist of 3 procedures: the solder paste screening, the placement of balls and the temperature reflow.
First, a thin layer of fresh solder paste is screened onto the ball pads. This solder paste acts as an adhesive agent for the ball and also supply extra flux to the joint. A cavity fixture must be used to hold the chip and the stencil for proper screening. Multi-chip fixture that can screen a dozen chips at the same time is used to speed up the operations.
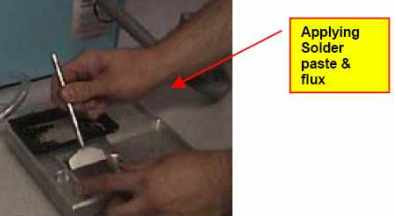
The next step is to screen the ball spheres onto the chip. A vacuum ball pickup/deposit fixture is used to pickup the spheres from the tray and release them onto the chip. The balls should sit properly and are loosely adhered to the pads after this process.
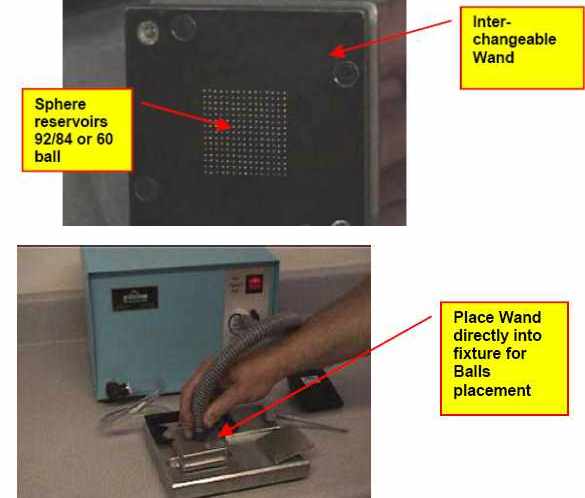
Next is the reflow process. The reflow process relies on the temperature profile setting. The temperature setting also depends on the construction of the spheres (ball), whether they are leaded or “no lead”.

Final Test and Package
Once the balls are “baked” onto the chips, final electrical test would be applied. This is generally done with functional DRAM tester with “tuning fork” type of socket. The tuning fork contact is a U shape forceps designed to grab hold of the solder ball for electrical contacts. Since different manufacturer have different chip package dimensions, different size inserts have to available to test the different package sizes.
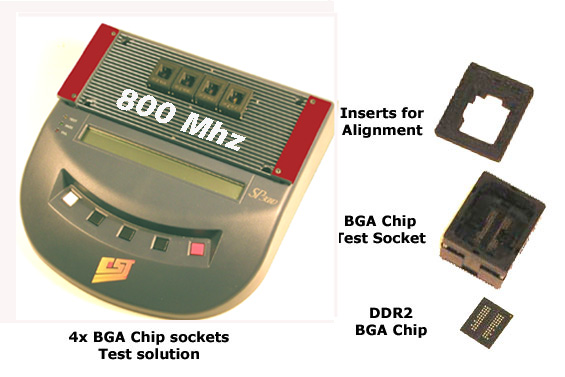
Since solder balls do oxidize quickly and builds an oxide coat that reduces the soldering characteristic of the ball, the chips should be vacuum sealed shortly after the reball process. The chips are usually put into trays and the entire tray is vacuum sealed into an anti-static bag. This completes the many steps of reballing the DDR2 memory chips.
Complexity of the Setup
An investment of tools is required in the DDR2 reball. Since DDR2 DRAM package comes in 20 different physical sizes, different fixture is required for each of the sizes. This includes the solder paste stencil, the cavity chip holder and the ball screening stencil. The ball pickup/deposit head would also need to be customized to each chip size for consistent performance.
Since test is an important step to ensure the reball chips will work, electronic microscope is required for visual inspections. A set of chip tester with pogo pin BGA sockets will be required for testing chips that had the balls removed. A tuning fork socket tester is also needed to do final test without damaging the balls. Since the chips are in different sizes, full set of 20 some socket inserts (size limiter) are required.
There is also the skill labor required. I have heard of 30 minutes process for reballing each chip. Yet, with the proper equipment and fully trained labor, this task can be achieved in an average of 10 minutes.
Price Cost Ratio for Reball
Whether an in-house DDR2 BGA reball would pay is purely based on simple mathematics. The first thing is to look at equipment amortization. What does it take to gather all the equipments, space and the training? How many chips can an operator do in a day? You then divide the cost of equipment and labor to per chip cost. If that is still attractive, you will then be able to come out ahead.
On the other hand, there is also a time/price risk factor involved. As DRAM prices fluctuates daily, your DRAM might lose its value while in inventory getting reballed. Yesterday’s 256Mbit DRAM might no longer fetch the same amount as today’s inventory or vise versa.
In House process vs Subcontract
When the labor and equipment investment cost is over the cost of subcontract repair, it is time to consider whether to do it in-house or just subcontract it out to some lower labor country. Use of off shore labor in this labor intensive process may allow substantial saving. It will avoid capital investment as well as long term maintenance and training.
However, you are also trading quick turnaround with a turn around of 1-2 weeks
By: DocMemory Copyright © 2023 CST, Inc. All Rights Reserved
|